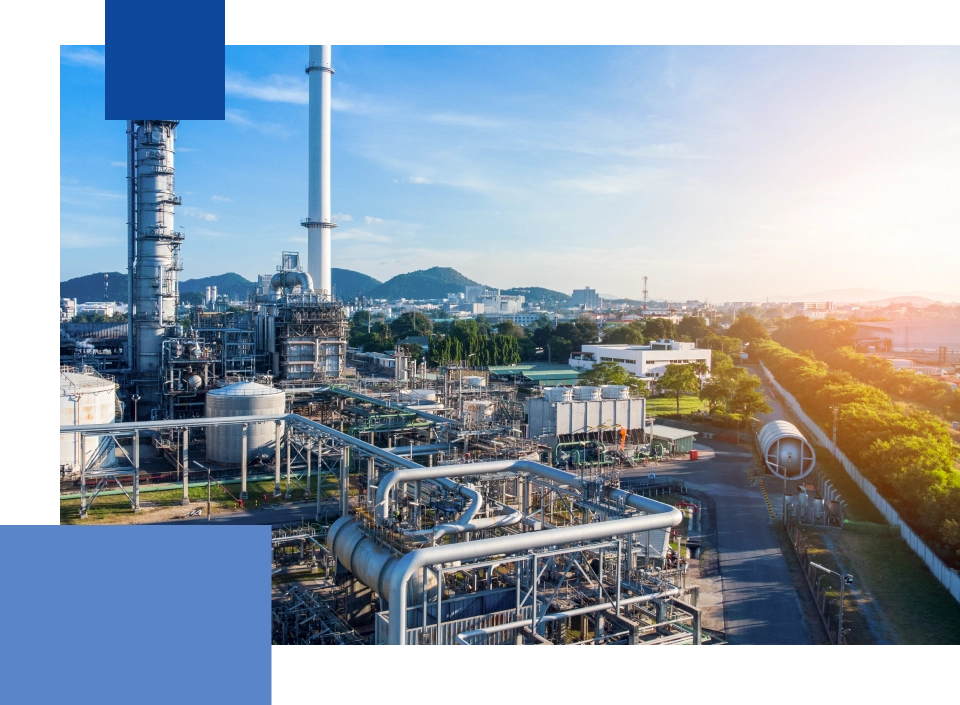
Battery Mixing (믹싱공정)
믹싱공정 개요
우리가 흔히 알고 있는 2차전지 배터리는 다양한 공정단계를 거쳐 제작되는데요.
크게 전극공정, 조립공정, 활성화공정, 팩공정 등 총 4가지 단계를 거치게 됩니다. 이 중 양극과 음극을 만드는 핵심 과정이 '전극 공정'인데요. 전극공정의 첫 단계가 바로 믹싱공정 (Mixing)입니다.
믹싱공정은 용어 그대로 양극과 음극을 만드는데 필요한 각종 원자재를 계량하여 혼합하는 과정을 말하는데요. 양극, 음극 각각의 가루형태 활물질에 바인더와 도전재, 용매를 섞어 슬러리 형태로 만들게 됩니다.
믹싱공정은 용어 그대로 양극과 음극을 만드는데 필요한 각종 원자재를 계량하여 혼합하는 과정을 말하는데요. 양극, 음극 각각의 가루형태 활물질에 바인더와 도전재, 용매를 섞어 슬러리 형태로 만들게 됩니다.
믹싱공정 구성요소 별 역할
믹싱공정의 구성요소 별 역할을 자세히 살펴보면 다음과 같습니다.
1
활물질은 양극, 음극에서 배터리의 전극반응을 활성화시켜주는 물질입니다. 2차전지인 리튬이온전지는 전압을 가해주는 양극에 주로 리튬산화물이 활물질로 사용됩니다.
2
도전재는 양극의 활물질의 전도성을 높여주는 역할을 하며, 바인더는 양극, 음극의 집전판인 알루미늄박과 동박에 활물 및 도전재가 잘 흡착될 수 있도록 도와주는 역할을 합니다.
3
첨가재의 경우 에너지의 밀도 향상, 충전속도 단축, 전지의 안정화 등을 위한 보완재로 사용되게 됩니다.
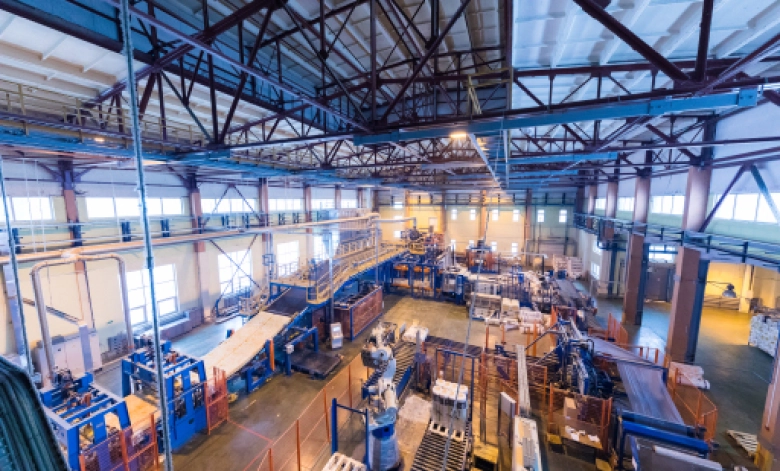
각 혼합재료에 사용되는 소재
활물질 - 양극
NCA, NCM, LCO,LFP, 음극 : 천연 흑연, 인조흑연
도전재 - 양극
카본블랙
바인더 - 양극
PVDP, 음극 : SBR/CMC
용매 - 양극
NMP, 음극 : 탈이온수, NMP
첨가재 - 양극
CNT, 음극 : 실리콘산화물, CNT
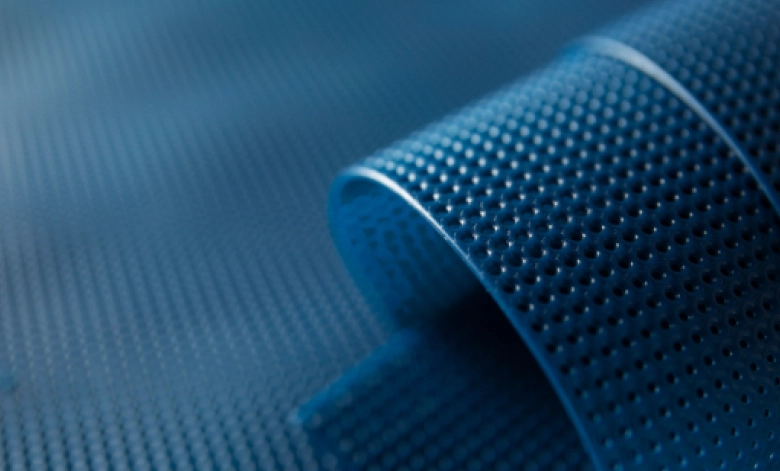
믹싱공정 작업과정
믹싱공정의 공정흐름은 다음과 같습니다.
1. 분체(Powder) 공급
각 계량호퍼에 바인더, 도전재, 활물질을 공급해줍니다.
2. 선분산(Pre Mixing)
단계별 믹서와 분산용매를 통해 믹싱과정을
거치게 됩니다.
3. 메인믹싱(Mixing)
각 재료의 혼합믹싱을 통해 슬러리형태로 만들게
됩니다.
4. 슬러리 저장 및 이송
만들어진 슬러리를 저장탱크에 저장하고 이후 단계인 코팅공정에서
사용될 수 있게 이송됩니다.
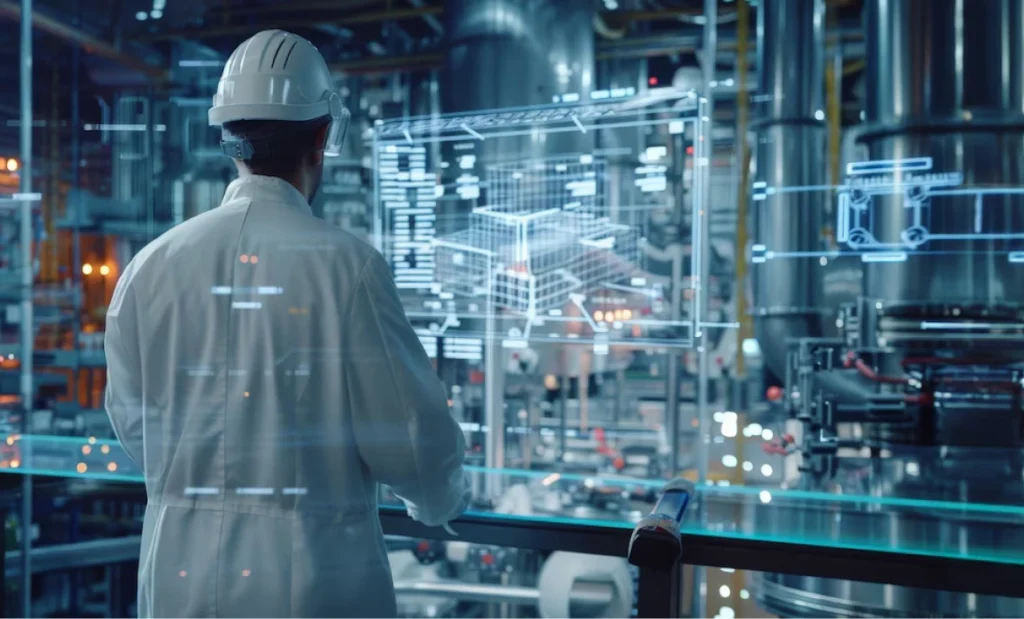
믹싱공정 세부공정
플래니터리밀을 사용한 혼합
전극 공정의 첫 과정인 믹싱 공정에서는 믹싱이라는 단어 그대로 양극 활물질과 음극 활물질을 섞습니다. 음극 활물질(음극재)은 결정구조가 약해 강한 전단 응력을 가하는기기를 사용할 수 없는데요. 그래서 밀가루를 반죽할때 사용하는 기계와 유사한 모습의 플래니터리밀(Planetary Mill) 기계를 사용해 믹싱 작업을 합니다.
바인더와 용매 조합
일반적으로 바인더는 폴리비닐리덴 플루오라이드(PVDF, Polyvinylidene fluoride)가 사용 되는데, 주로 NMP용매와 함께 사용됩니다. PVDF와 NMP조합은 접착력이
우수한 데다, 도전재의 분산을 용이하게 하고, 산화 / 환원반응에도 안정적인 장점이 있습니다. 최근에는 에너지 밀도를 더 높이기 위해, 활물질 함량을 높이고 바인더 함량을 줄일 수 있는SBR이나 CMC를 사용하기도 합니다.
안정적인 접착력 유지를 위한 바인더 첨가
활물질 입자간 접착력을 높이기 위해 바인더를 첨가하는데요. 전극에 투입되는
바인더는 전해질과의 접촉과 전극내에서 일어나는 산화환원반응에서도 접착력이
고정될 수 있는 안정적인 특성을 지녀야 합니다.
활물질과 도전재 융합
활물질의 각 입자 크기가 어떤 비율로 분포 해 있는지(입도 분포)가 믹싱 공정과
전극의 품질에 영향을 끼치기도 하는데 너무 크거나 작은 활물질은 분진을 일으킬 수 있어 제거해야합니다. 또, 활물질에 점 접촉(point contact)이 많아지면 사이사이
빈틈들로 인해 용량이 줄어들 수 있어 전자 전도 물질인 도전재를 넣어 빈틈 사이를
메꿔야 합니다.
정리하면, 믹싱 공정에서는 활물질에 바인더와 용매, 도전재를 추가하여 섞고, 그 결과 중간재인
슬러리가 만들어집니다. 슬러리를 만드는 이유는 집전체인 알루미늄(양극)이나 구리(음극)에
코팅하기 적합안 액체상태이기 때문입니다. 추가로 슬러리에 이물질이 혼입되지 않도록 믹서기 속
관리도 철저히 해야 합니다.
믹싱공정 주의사항
믹싱공정의 경우 여러 혼합물들이 정량의 배합으로 균일하게 섞일 수 있도록 하고 이물질이 들어가지 않도록 하는 품질 관리 기술이 중요하게 됩니다.
또한 생산성 향상을 위해 대용량, 생산 속도 향상이 혼합 공정 장비의 주요 경쟁력입니다.
또한 생산성 향상을 위해 대용량, 생산 속도 향상이 혼합 공정 장비의 주요 경쟁력입니다.
믹싱공정의 경쟁력
믹서의 용량
얼마나 많은 양을 한 번에 생산할 수 있는지가 중요 경쟁요소입니다. 생산성과
직결되는 문제이고, 이 생산성은 생산비용과 직결되기 때문입니다.
믹서의 내마모성과 내구성
결함으로 인해 발생하는 생산성 감소는 곧 매출과 연결되기 때문에 믹서 유지관리도 필수항목입니다.
믹서의 생산시간과 균질함
얼마나 빠른시간안에 얼만큼의 균질한 슬러리를 생산하는 것이 큰 경쟁력이 되므로
믹싱공정 전체시스템을 잘 구축해야 합니다.
믹싱공정의 단순화와 시스템 최적화
생산성에 영향을 주는 외부변수 최소화를 위해 공정 단순화를 시행하고
시스템최적화를 통한 일관성있는 생산성 확보에 주력해야 합니다.
위와 같이 연속식 믹서는 재료의 혼합 및 분산기능을 통해 응용 범위가 광범위합니다.
제조업을 비롯한 다양한 산업의 재료 혼합 수요를 충족시켜 줄 수 있고 신규산업의 모태가 되어
향후 발전가능성이 클 것으로 판단됩니다.