MR(Maintenance Reality Solution)
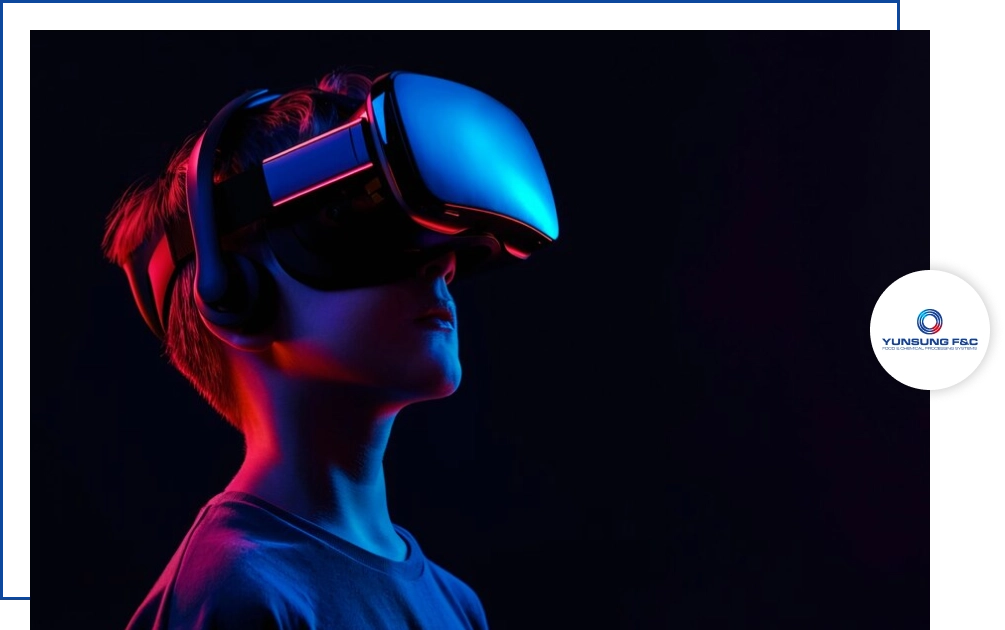
What is MR (Maintenance Solution)?
MR (Maintenance Solution) is a solution that utilizes AR (Augmented Reality) and VR (Virtual Reality) technologies to share real-time work situations, maintenance tasks, fault causes, and technical documents.
Additionally, it can be used to enhance the technical capabilities of junior technicians through virtual learning and training, as well as to transfer expert know-how. MR provides immediate guides tailored to the work situation, thereby strengthening the capabilities of workers, improving productivity, and increasing equipment uptime.
Additionally, it can be used to enhance the technical capabilities of junior technicians through virtual learning and training, as well as to transfer expert know-how. MR provides immediate guides tailored to the work situation, thereby strengthening the capabilities of workers, improving productivity, and increasing equipment uptime.
Real-Time Monitoring
Unexpected machine failures in industrial settings can lead to production stoppages and significant financial losses. To address this issue, the MR solution monitors the condition of machines in real-time through data-based analysis. This allows for the immediate detection of abnormal signs in machines and the ability to plan maintenance systematically based on the severity of the anomalies. Furthermore, maintenance costs can be differentiated according to the level of abnormalities, enabling the establishment of an efficient maintenance management system.
Components of the MR System
The MR system is composed of the following components:
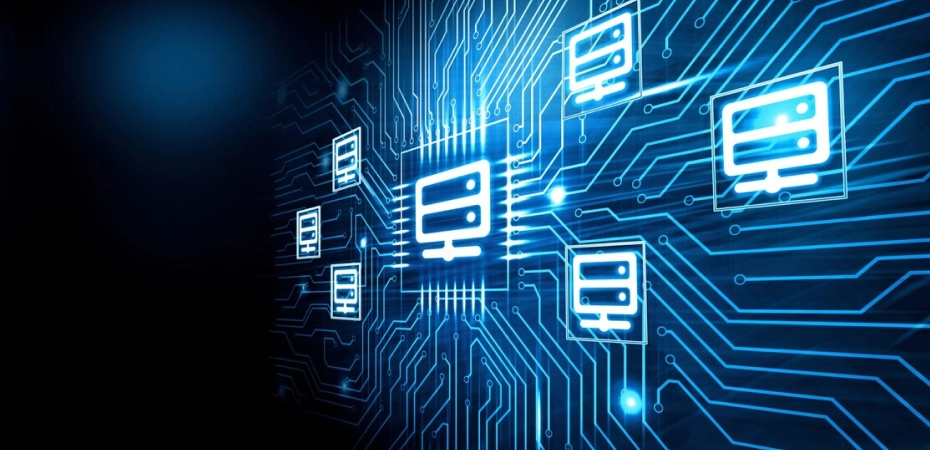
Sensors and IoT Devices
Collect numerical data such as temperature, vibration, and pressure through sensors attached to equipment.
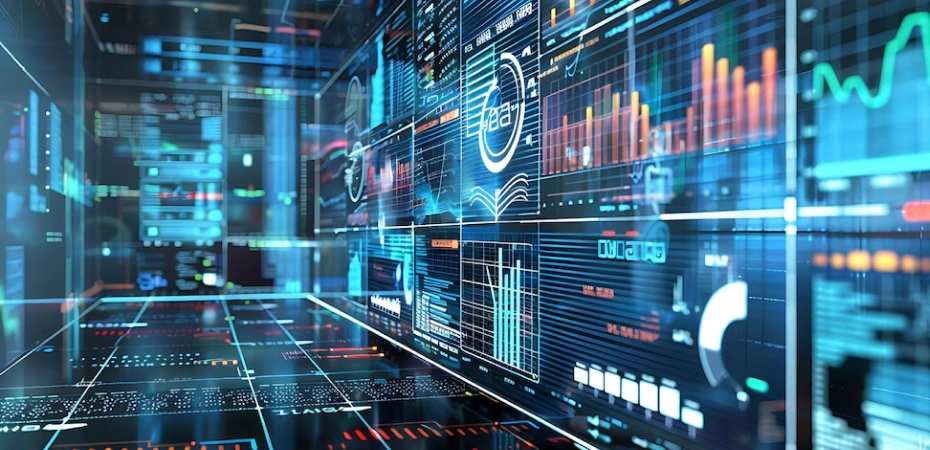
Data Analysis Platform
Analyzes the collected data to assess the condition of machines
and predict whether maintenance is needed.
and predict whether maintenance is needed.
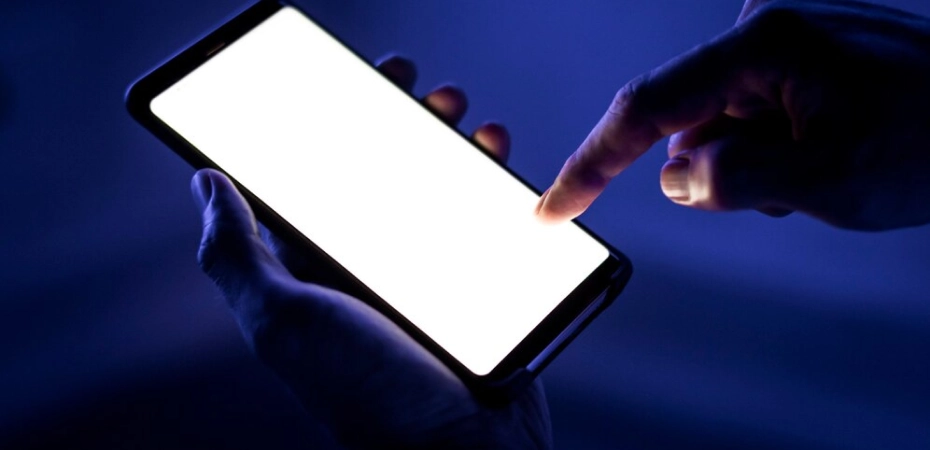
Data Analysis Platform
Personnel receive real-time notifications from installed sensors via a connected mobile app and can respond immediately on-site when abnormalities occur.
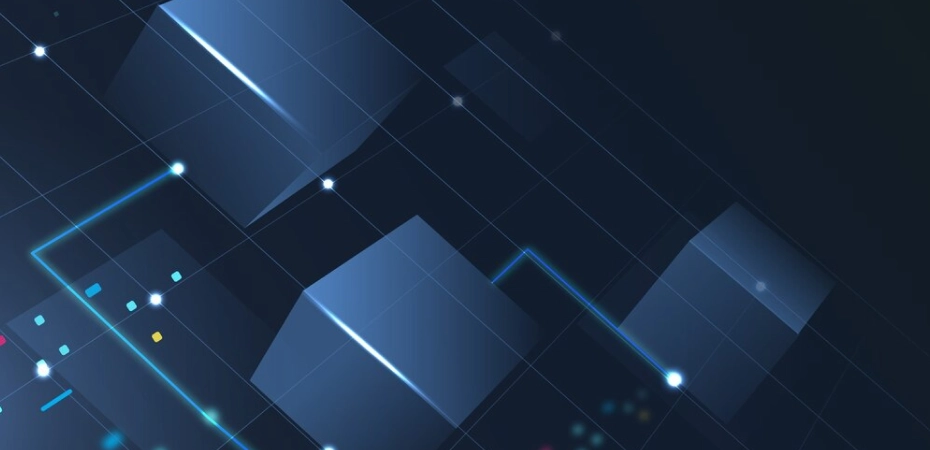
Integrated Management System
Enables rapid response to various abnormal situations through a unified management system and allows for quick verification of corrective actions.
Key Features of MR

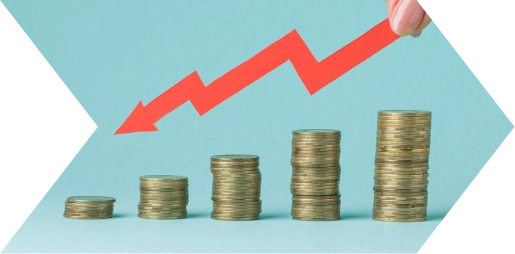
Minimizes Spatial and Temporal Constraints, Reduces Time and Costs
Enables immediate on-site response and problem-solving through remote collaboration. The system can remotely monitor the status of equipment and quickly identify the causes of issues when problems arise.
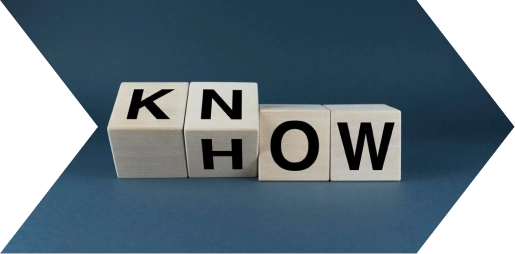
Transfer of Expert Know-How Through MR Training
Enhances efficiency through continuous remote collaboration between domestic technicians and overseas experts. MR training allows the transfer and internalization of specialized skills and know-how.
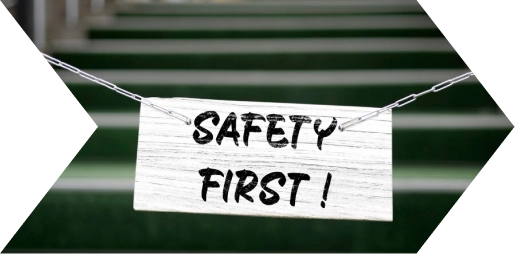
Increases Safety Through Pre-Work Education for Hazardous Machine Operations
Improves worker proficiency through MR-based disassembly and assembly training. Simulations before actual work can identify and mitigate potential risks, allowing workers to assess the risks of tasks before performing them.
Expected Benefits of Implementing MR

Improved System Uptime
Minimizes system downtime through preventive maintenance aimed at forecasting and preventing malfunctions. Maintaining consistent system uptime helps in forecasting predictable production volumes.

Reduced Maintenance Costs
Reduces recovery costs after failures through MR and achieves long-term cost savings over the entire lifecycle by implementing preventive maintenance.

Enhanced Safety
Enables immediate on-site response and problem-solving through remote collaboration. The system can remotely monitor equipment status and swiftly identify the causes of issues when problems occur.

Increased Productivity
Improves productivity by maintaining consistent production management and patterns through predictable risk management and response enabled by MR. Increased productivity directly contributes to higher profits, which is a key focus in production management.
Applications of MR
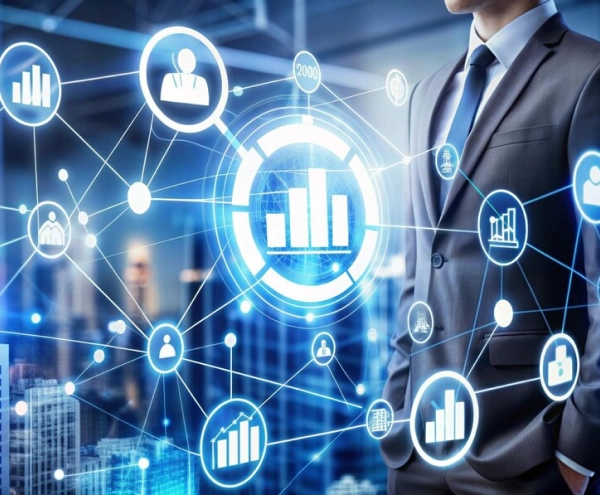
Sensors and IoT Devices
· Real-time sharing of situations and instructions between remote managers and on-site workers.
· Emergency response through collaboration between remote experts and workers via smart glasses, with rapid transmission of expert work guides.
· Remote experts can perform real-time pointing, drawing on shared screens, and share technical documents to facilitate faster task completion.
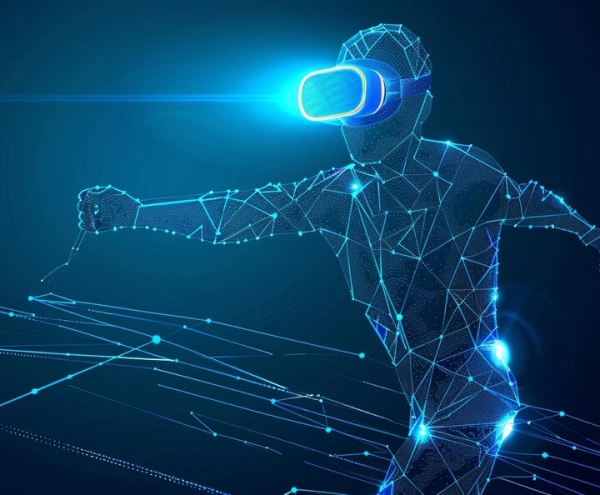
Virtual Learning
· Enhances the proficiency of junior technicians through VR technology, significantly improving training effectiveness.
· Conducts pre-learning of disassembly and assembly of complex VR 3D equipment to minimize errors during actual work.
· Enables proficient task handling by learning the structure and functions of work equipment through various devices.
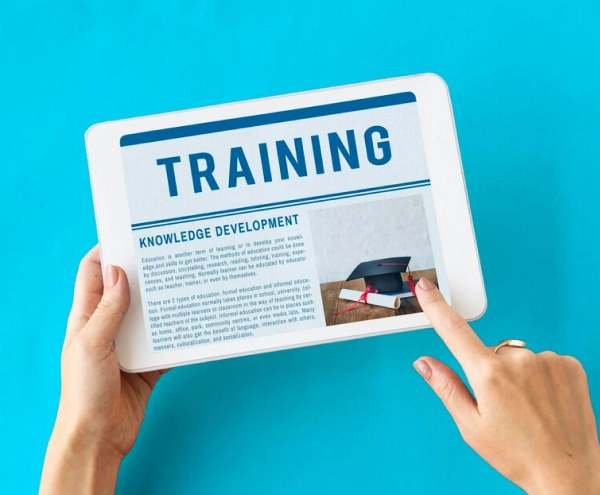
Virtual Training
· Conducts real-time education and training by connecting and synchronizing multiple learners and instructors in a VR space.
· Provides training that conveys instructors' demonstrations and know-how in equipment disassembly/assembly and checks practical exercises.
· Implements effective virtual training through smooth real-time sharing and content delivery between instructors and learners, as well as among learners themselves.
Future of the MR System
The MR (Maintenance Solution) system has established itself as an essential element of production management. By enabling efficient maintenance management and swift, data-driven decision-making, it maximizes corporate profits.
However, successful implementation requires a clear understanding of the technology concept, investment, and a commitment to practical application, supported by technological advancements. The development of MR systems is expected to significantly impact the stable operation of industries through increased smartization and automation in the future.
However, successful implementation requires a clear understanding of the technology concept, investment, and a commitment to practical application, supported by technological advancements. The development of MR systems is expected to significantly impact the stable operation of industries through increased smartization and automation in the future.
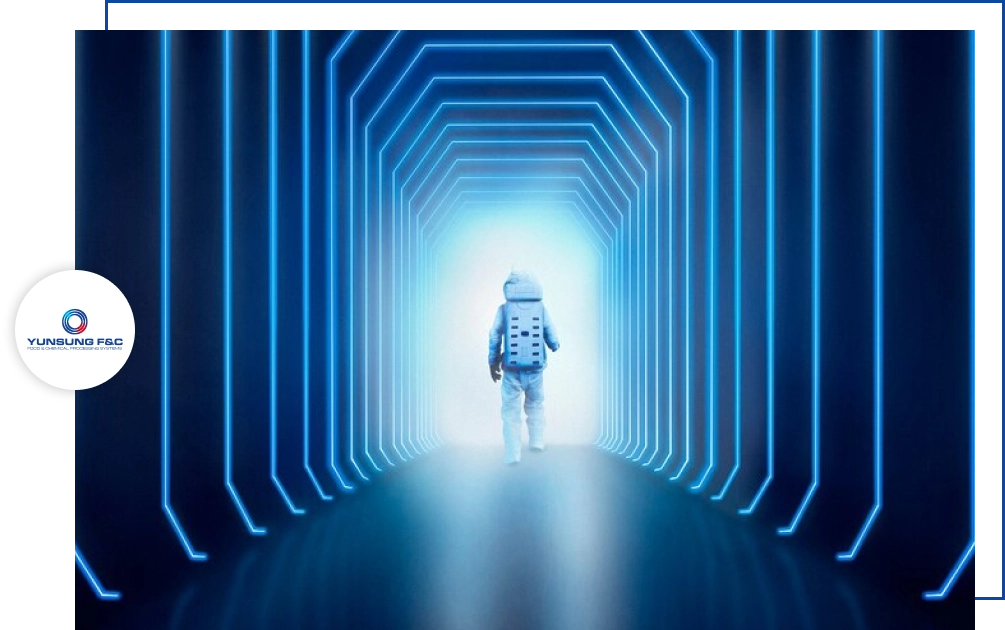