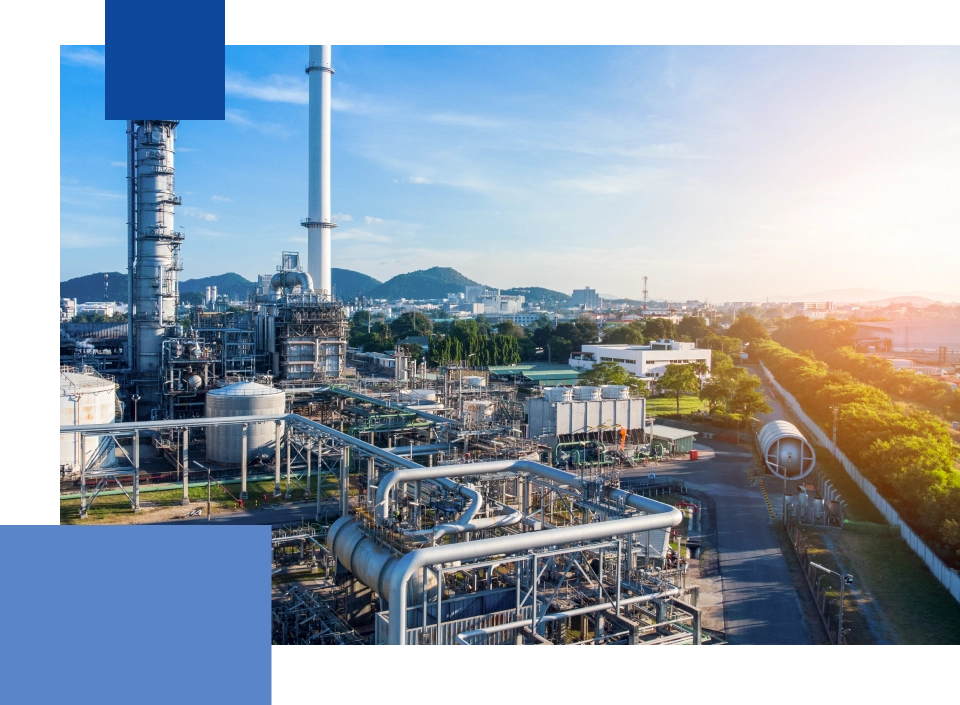
Battery Mixing
Overview
The secondary batteries we commonly know go through various processing stages during their production. There are four main stages: electrode processing, assembly processing, activation processing, and pack processing. Among these, the key process of making the cathode and anode is the 'electrode processing.' The first step in electrode processing is the mixing process (Mixing).
The mixing process, as the term suggests, refers to the process of measuring and mixing various raw materials needed to make the cathode and anode. For both the cathode and anode, the powder-form active materials are mixed with a binder, conductive agent, and solvent to create a slurry.
The mixing process, as the term suggests, refers to the process of measuring and mixing various raw materials needed to make the cathode and anode. For both the cathode and anode, the powder-form active materials are mixed with a binder, conductive agent, and solvent to create a slurry.
Roles of Each Component in the Battery Mixing Process
The roles of each component in the mixing process are detailed as follows.
1
The active material activates the electrode reactions in the cathode and anode of the battery. In lithium-ion secondary batteries, lithium oxides are primarily used as the active material in the cathode, where the voltage is applied.
2
The conductive agent enhances the conductivity of the active material in the cathode, while the binder helps the active material and conductive agent adhere well to the current collectors, which are aluminum foil for the cathode and copper foil for the anode.
3
Additives are used as supplementary materials to improve energy density, reduce charging time, and stabilize the battery.
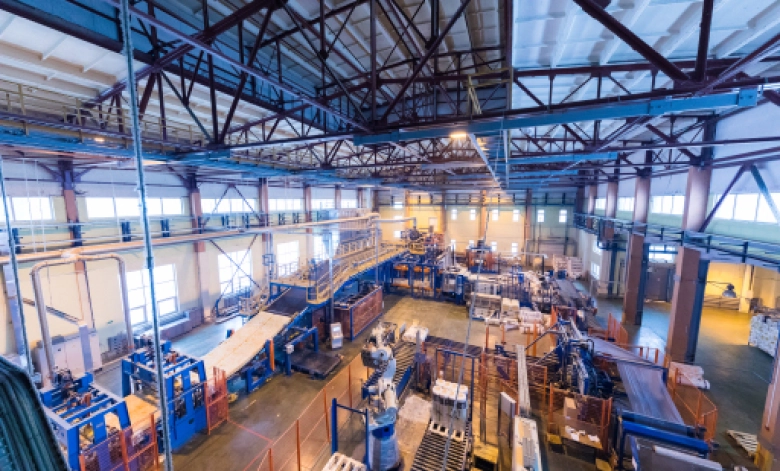
Materials used for each mixed component are as follows
Active Material - Cathode
NCA, NCM, LCO, LFP, Anode: Natural Graphite, Synthetic Graphite
Conductive Agent - Cathode
Carbon Black
Binder - Cathode
PVDP, Anode : SBR/CMC
Solvent - Cathode
NMP, Anode : Deionized Water, NMP
Additives - Cathode
CNT, Anode : Silicon Oxide, CNT
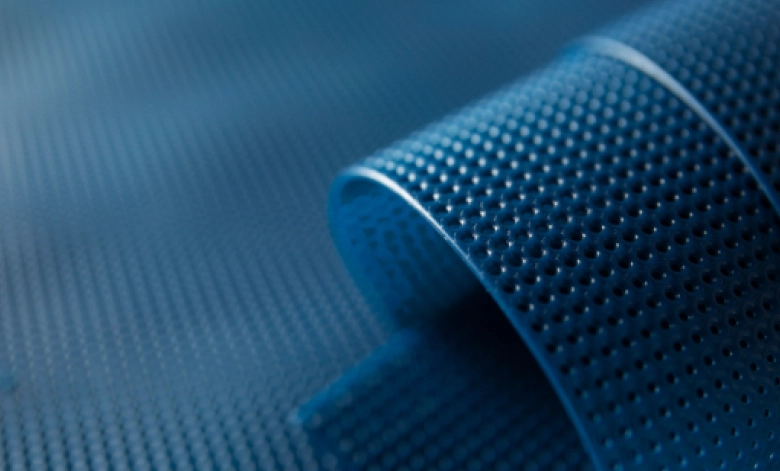
Battery Mixing Process Workflow
The process flow of the mixing procedure is as follows.
1. Powder Supply
Supply binder, conductive agent, and active material to each metering hopper.
2. Pre Mixing
The mixing process is carried out through step-by-step mixers and dispersion solvents.
3. Main Mixing
The materials are mixed together to form a slurry.
4. Save and transfer slurry
The prepared slurry is stored in a storage tank and then transferred to the next stage, the coating process.
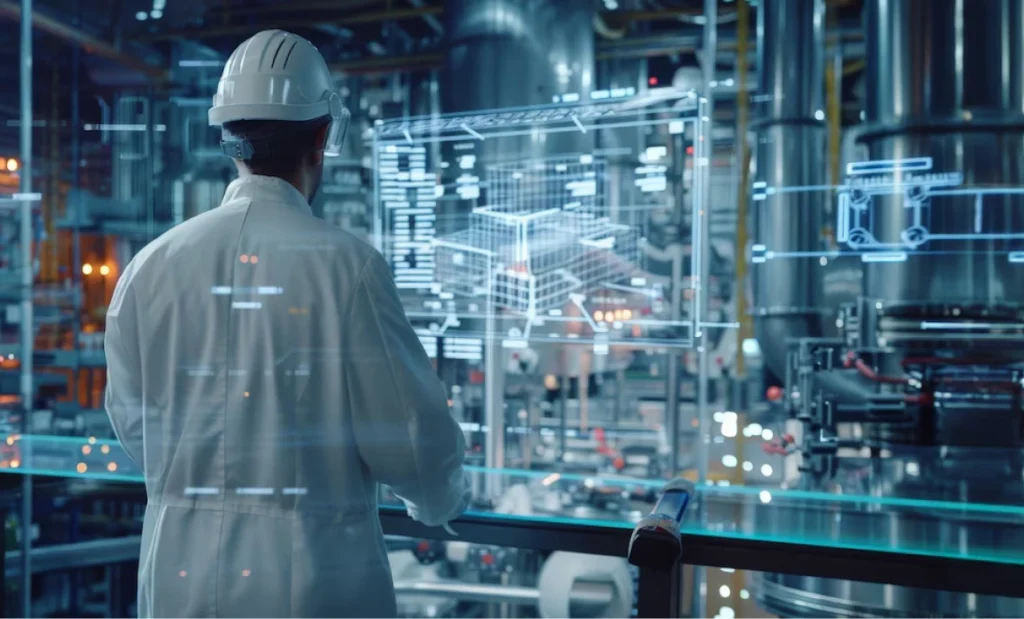
Detailed Processes of the Battery Mixing Procedure
Mixing Using a Planetary Mill
In the first step of the electrode process, the mixing process, the term "mixing" precisely describes the action of blending cathode and anode active materials. The anode active material (anode material) has a fragile crystal structure and cannot withstand strong shear stress. Therefore, a planetary mill, a machine similar to those used for kneading dough, is used for the mixing operation.
Combination of Binder and Solvent
Typically, the binder used is polyvinylidene fluoride (PVDF), which is mainly used in combination with the NMP solvent. The PVDF and NMP combination provides excellent adhesive properties, facilitates the dispersion of the conductive agent, and is stable during oxidation/reduction reactions. Recently, to increase energy density, materials like SBR (styrene-butadiene rubber) or CMC (carboxymethyl cellulose) are also used. These materials allow for a higher content of active material and a lower content of binder.
Addition of Binders to Maintain Stable Adhesive Properties
To enhance the adhesion between active material particles, binders are added. The binders used in electrodes must possess stable properties, ensuring that their adhesive strength is maintained during contact with the electrolyte and throughout the oxidation-reduction reactions occurring within the electrode.
Fusion of Active Material and Conductive Agent
The particle size distribution (PSD) of the active material, which indicates the proportion of particles of different sizes, affects the mixing process and the quality of the electrode. Particles that are too large or too small can generate dust and must be removed. Additionally, if there are many point contacts among the active material particles, the resulting voids can reduce the battery's capacity. To address this, conductive agents are added to fill these gaps, enhancing the overall electron conductivity and ensuring a more efficient battery performance.
To summarize, in the mixing process, binders, solvents, and conductive agents are added to the active material and mixed together to create an intermediate product called slurry. The reason for making slurry is that its liquid state is suitable for coating onto the current collectors, which are aluminum for the cathode and copper for the anode. Additionally, it is crucial to maintain strict control over the mixer to prevent the incorporation of foreign substances into the slurry.
Precautions for the Battery Mixing Process
In the mixing process, quality control techniques are crucial to ensure that various mixtures are uniformly blended in precise proportions and to prevent the introduction of foreign substances.
Additionally, for improving productivity, large capacity and increased production speed are key competitive advantages of mixing process equipment.
Additionally, for improving productivity, large capacity and increased production speed are key competitive advantages of mixing process equipment.
Competitive Advantages of the Mixing Process
Mixer Capacity
The amount that can be produced in a single batch is a key competitive factor. It is directly related to productivity, and this productivity is directly tied to production costs.
The wear resistance and durability of the mixer
Productivity reduction due to defects is directly linked to revenue, making mixer maintenance an essential task.
The production time and homogeneity of the mixer
The ability to produce a large amount of homogeneous slurry in a short time is a significant competitive advantage, so it is essential to establish a well-structured mixing process system.
Simplification and optimization of the mixing process system
To minimize external variables that affect productivity, process simplification should be implemented, and efforts should be focused on ensuring consistent productivity through system optimization.
Continuous mixers have a wide range of applications in the mixing and dispersion of materials. They can meet the material mixing demands of various industries, including manufacturing, and hold significant potential for future development as the foundation for new industries.