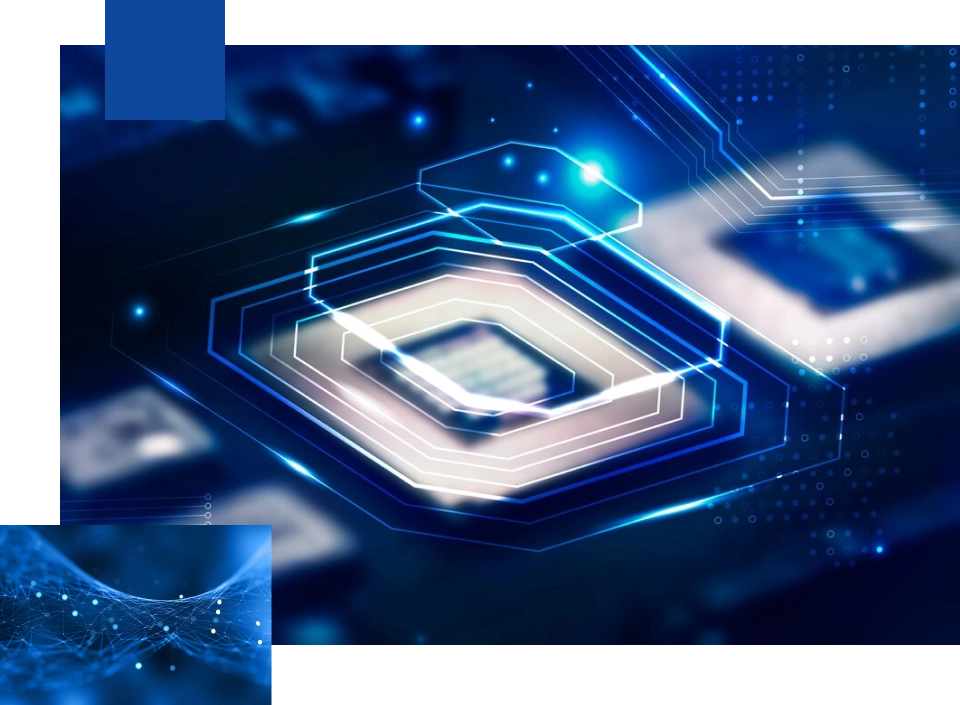
CONTINUOUS SLURRY MIXER
Overview
A Continuous Mixer, also known as an In-Line Mixer, is a type of industrial mixing equipment used for continuous and uninterrupted mixing and uniform dispersion of materials. It is particularly useful in the initial stages of manufacturing cathodes and anodes for secondary batteries, where it uniformly mixes and disperses active materials, conductive agents, and binders. Additionally, continuous mixers are widely used in industries such as chemicals, food, pharmaceuticals, construction materials, and other sectors that require mixing and dispersion.
Components
The components of a continuous mixer include storage chambers and metering systems for powders and fluids, a continuous mixing device where agitation and dispersion occur, and a discharge storage unit for the mixed output. A control system operates these mechanical and structural systems. To ensure basic mixing performance, the process should be wet-based, and PID control (Proportional Integral Derivative Control) can be used for precise fluid supply per unit time. Powders, such as active materials, can be accurately supplied using LIW (Loss-in-Weight) control. Continuous mixers generally adopt a twin-screw extruder design with two screws arranged in parallel, most commonly using closely interlocking, co-rotating screws.
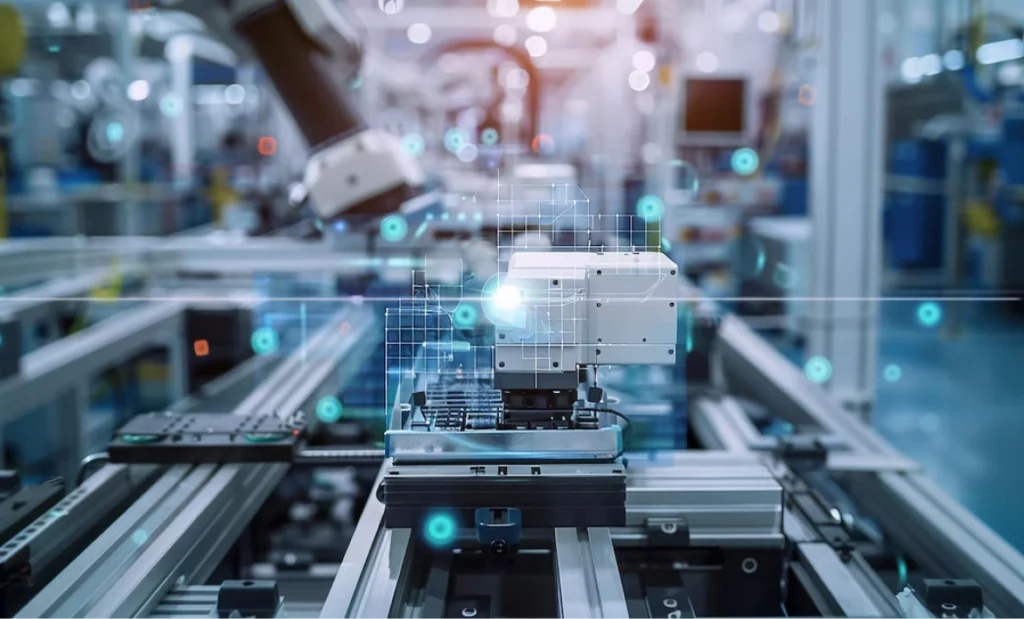
Mechanism
In a continuous mixer, agitation/dispersion and transportation of the medium must occur simultaneously. The twin-screw extruder’s working principle encompasses both these functions. Fluids and powders introduced into the mixer are transformed into a slurry through the high shear rate and excellent dispersion and mixing capabilities of the co-rotating twin-screws. This slurry is then transported forward through the screws. The screws perform both transportation and kneading functions, and optimal mixing performance and maximum production capacity can be achieved by adjusting the number of screw elements, their arrangement, and the rotation speed.
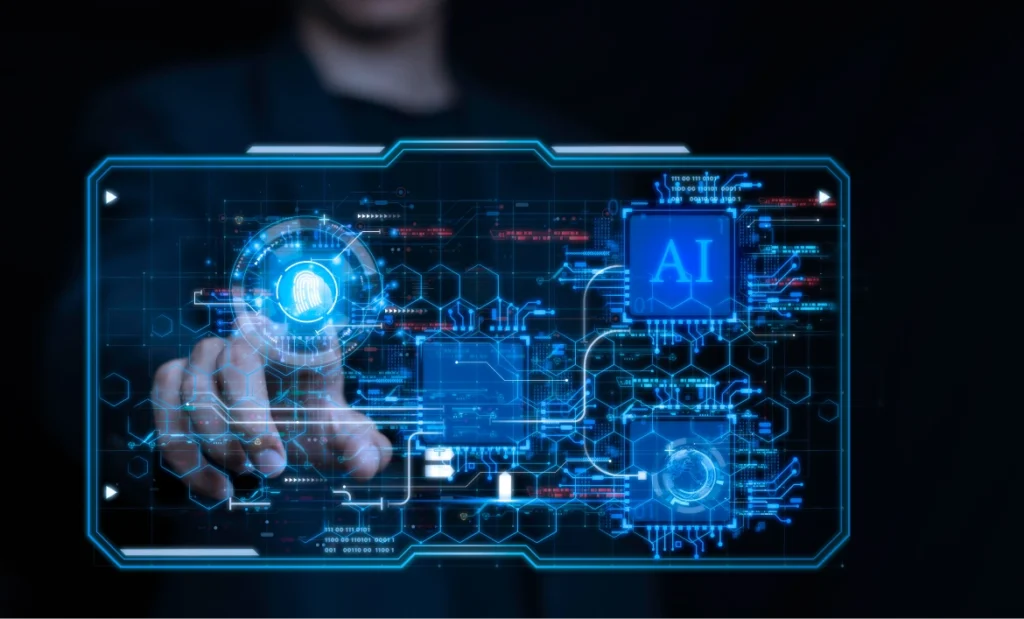
Features
01
Continuous Operation: Enhances production efficiency due to uninterrupted operation.
02
Uniform Dispersion and Mixing: Ensures stable product quality through consistent dispersion and mixing.
03
Space Efficiency: Occupies a small footprint, saving space.
04
Since there is no stopping section, you can save time and labor costs.
05
High Integration: Reduces power consumption due to the high integration of equipment and processes.
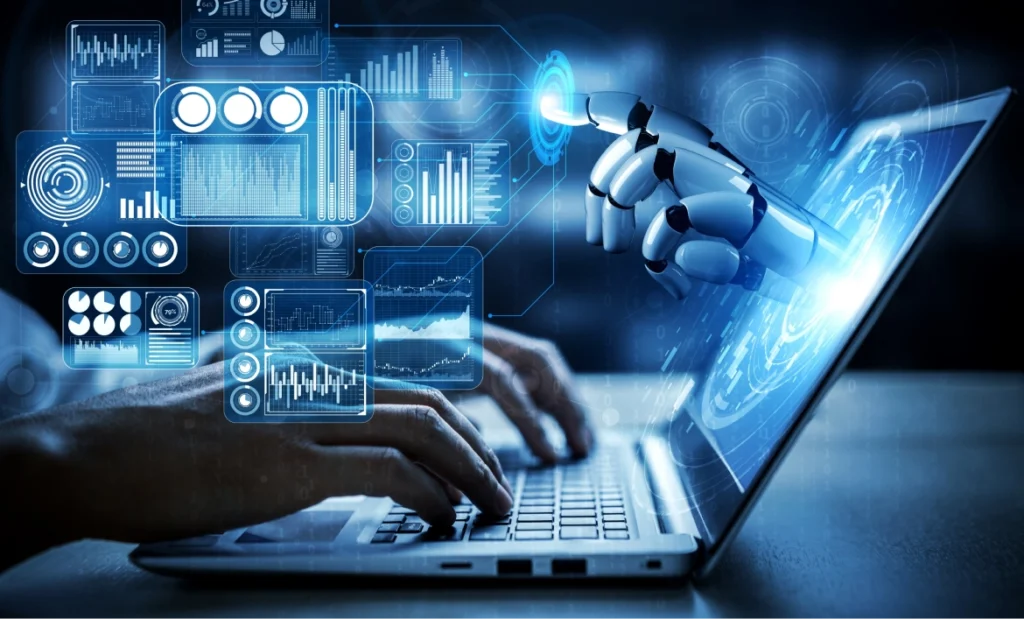
Applications of Continuous Mixers
Continuous mixers are utilized in various fields, especially in the chemical, food, pharmaceutical, and construction material industries.
Chemical Industry: Frequently used in the mixing and dispersion processes of granular, powder, liquid, and other materials in the production of fertilizers, plastics, rubbers, and more. They can be used in the production processes of chemical raw materials, pigments, dyes, colloids, and other chemical substances, improving product quality through uniform agitation.
Food Industry: Commonly used in the production of powdered food additives, seasonings, dry mixtures, etc. They are used for agitating food ingredients like seasonings, jams, doughs, and sauces to ensure consistent taste and enhance production efficiency.
Pharmaceutical Industry: Typically used in the mixing and manufacturing of pharmaceuticals, ensuring uniform dispersion of drug components and improving drug solubility and stability.
Construction Material Industry: Frequently used in the production processes of cement, lime, and other construction materials. Ensures uniform agitation of materials, thereby enhancing quality.
Continuous mixers have a wide range of applications in the mixing and dispersion of materials. They can meet the material mixing demands of various industries, including manufacturing, and hold significant potential for future development as the foundation for new industries.